Dave Chukwudulue is the General Manager of Transit Support Services (TSS) in charge of the newly opened TSS auto assembly facility located in Enugu state. He spoke on different sections of the facility which is a huge investment, after a facility tour by Transport Day’s Frank Kintum
Modern facility, but under-utilised
We have a very modern, brand new assembly line installed for the assembling of light duty, medium duty and heavy duty trucks of every capacity. All have been tested and confirmed that we can produce and assemble them here on this line.
Then, we have provision also for the assembling of semi-trailer buckets, three axles from SKD up, is also installed. We have assembled Forland light and medium duty trucks of various per loads and capacities.
We have assembled Shacman heavy duty trucks and medium duty lorries, we have assembled here on ground with the equipment that I pointed out to you earlier, Asian Star luxury buses of 53 passenger seats. We have also assembled here the Baw pilot minibuses of 16 passenger capacity. That is what we have here.
Currently, our tripod products consist of Shacman heavy duty trucks and medium duty lorries, then the Forland light duty trucks and then the semi-trailer, TSS Semi-trailer of 50 tons per load capacity.
How do you acquire your raw materials?
A lot of the materials come from the local vendors and suppliers, but the basic components come from China as imported CKD components, then we build up.
Staff
We did some bit of backward integration going back to our parent company which is ABC Transport Plc for some staff, and then in the auto industry to source other experienced technical people either companies that we have worked with in the past or through our contacts in the industry.
Lull in Activities in the plant
I think that is economy imposed, the downturn in the economy has affected us negatively just like it has affected every other automobile company negatively. The lack of clear disparity between the import duties on fully built vehicles and CKD and SKD components has made local assembly activities unattractive.
Capacity of the plant
Annual capacity depends on what we have on ground. The order we have on hand. As you can see from the new plant layout, we are equipped to do double shift if we have to. So, if we have an unlimited order on our hands, yes. Sure. We can do 2 trucks a day. And also do double shifts.
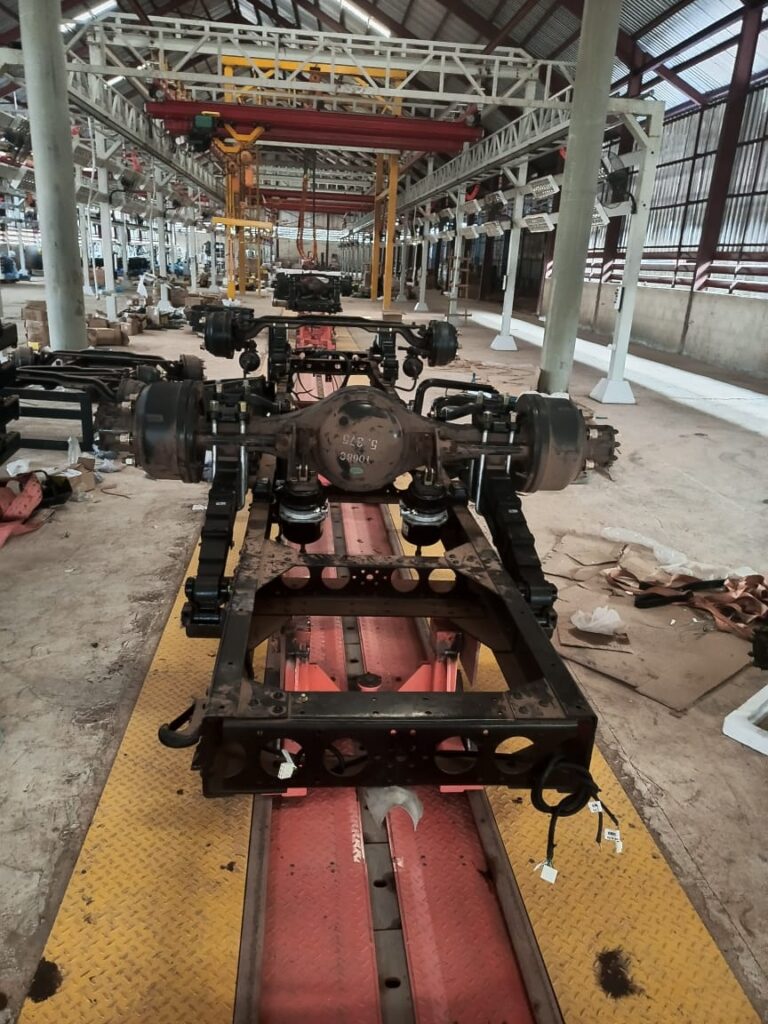
How do you think the auto industry can be improved?
Let there be a clearly defined auto policy. One that would clearly define and show clear discrepancy between fully built units and SKD and CKD components of the same vehicle.
There should be restriction, the economy should not be thrown open for every briefcase business man to import anything fully built from wherever without check and balances, it is killing the auto industry. And then of course, increasing negatively the unemployment level of the economy. So many auto companies were forced to lay off staffs for some time now because it does not make sense for them to do local assembly when they can import fully built units like every auto company, and there should be government patronage.
We know who the auto assemblers are. If government wants to buy certain capacity of vehicles, they can find out from them or invite the auto assemblers to come show proof of what they can do. The Customs and Ministry of Finance can go round periodically, at least, they come here so they know what we are doing and they know our capacities.
That is what kept Mercedes and ANAMMCO those days. We (ANAMMCO) used to have Ministry of Defence orders.